Do hàm lượng các chất độc hại như tro, nitơ và lưu huỳnh trong sinh khối thấp hơn so với năng lượng khoáng, nên nó có đặc điểm là trữ lượng lớn, hoạt tính cacbon tốt, dễ bắt lửa và các thành phần dễ bay hơi cao. Do đó, sinh khối là nhiên liệu năng lượng rất lý tưởng và rất phù hợp cho việc chuyển đổi và sử dụng trong quá trình đốt cháy. Tro còn lại sau khi đốt sinh khối rất giàu các chất dinh dưỡng cần thiết cho cây trồng như phốt pho, canxi, kali và magiê, nên có thể được sử dụng làm phân bón cho cây trồng. Với trữ lượng tài nguyên khổng lồ và những lợi thế tái tạo độc đáo của năng lượng sinh khối, hiện nay năng lượng sinh khối được các nước trên thế giới coi là một lựa chọn quan trọng cho việc phát triển năng lượng mới quốc gia. Ủy ban Phát triển và Cải cách Quốc gia Trung Quốc đã nêu rõ trong "Kế hoạch Thực hiện Sử dụng Toàn diện Rơm rạ trong Kế hoạch 5 năm lần thứ 12" rằng tỷ lệ sử dụng toàn diện rơm rạ sẽ đạt 75% vào năm 2013 và phấn đấu vượt 80% vào năm 2015.
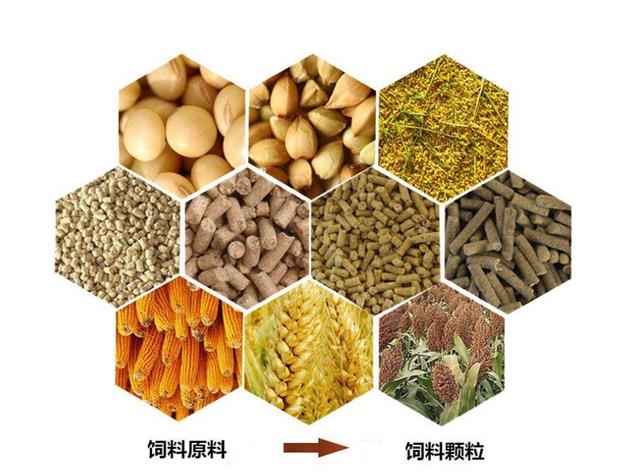
Việc chuyển đổi năng lượng sinh khối thành năng lượng chất lượng cao, sạch và tiện lợi đã trở thành một vấn đề cấp bách cần giải quyết. Công nghệ cô đặc sinh khối là một trong những cách hiệu quả để nâng cao hiệu quả đốt năng lượng sinh khối và tạo điều kiện thuận lợi cho việc vận chuyển. Hiện nay, trên thị trường trong và ngoài nước có bốn loại thiết bị tạo hình đặc phổ biến: máy đùn hạt xoắn ốc, máy dập hạt piston, máy tạo hạt khuôn phẳng và máy tạo hạt khuôn vòng. Trong số đó, máy tạo viên khuôn vòng được sử dụng rộng rãi do các đặc tính như không cần gia nhiệt trong quá trình vận hành, yêu cầu độ ẩm nguyên liệu rộng (10% đến 30%), công suất máy lớn, mật độ nén cao và hiệu quả tạo hình tốt. Tuy nhiên, các loại máy tạo viên này thường có những nhược điểm như dễ mòn khuôn, tuổi thọ ngắn, chi phí bảo trì cao và việc thay thế bất tiện. Để khắc phục những nhược điểm trên của máy tạo viên khuôn vòng, tác giả đã thiết kế một cải tiến hoàn toàn mới về cấu trúc khuôn tạo hình và thiết kế một loại khuôn tạo hình có tuổi thọ cao, chi phí bảo trì thấp và bảo trì thuận tiện. Trong khi đó, bài viết này đã tiến hành phân tích cơ học khuôn tạo hình trong quá trình làm việc của nó.
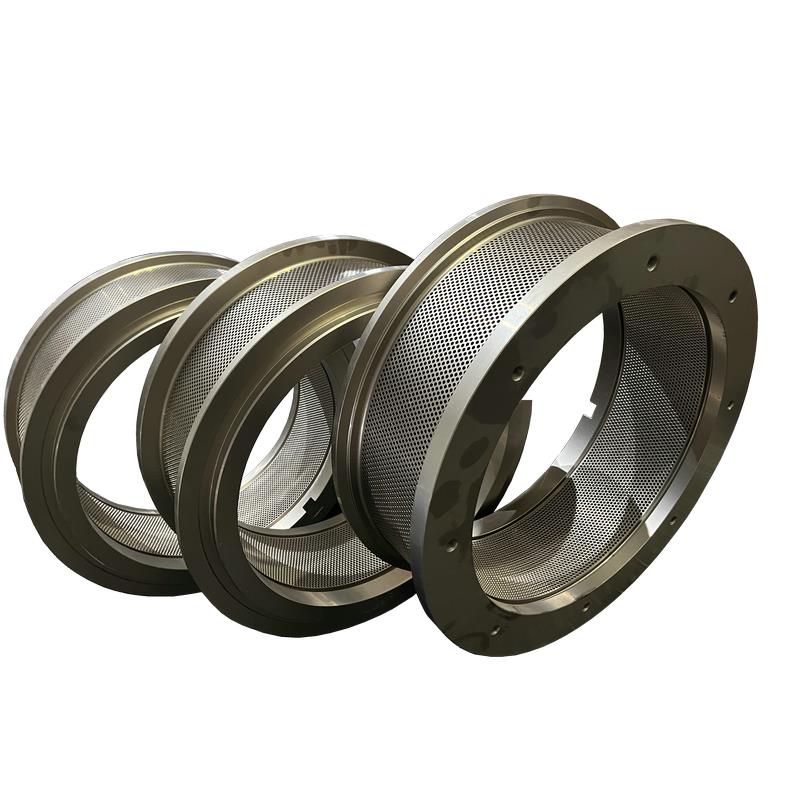
1. Thiết kế cải tiến kết cấu khuôn định hình cho máy nghiền khuôn vòng
1.1 Giới thiệu về quy trình đùn ép:Máy ép viên khuôn vòng có thể được chia thành hai loại: thẳng đứng và nằm ngang, tùy thuộc vào vị trí của khuôn vòng; Theo hình thức chuyển động, nó có thể được chia thành hai hình thức chuyển động khác nhau: con lăn ép chủ động với khuôn vòng cố định và con lăn ép chủ động với khuôn vòng dẫn động. Thiết kế cải tiến này chủ yếu nhắm vào máy ép viên khuôn vòng với con lăn áp lực chủ động và khuôn vòng cố định làm hình thức chuyển động. Nó chủ yếu bao gồm hai phần: cơ cấu vận chuyển và cơ cấu hạt khuôn vòng. Khuôn vòng và con lăn áp lực là hai thành phần cốt lõi của máy ép viên khuôn vòng, với nhiều lỗ khuôn tạo hình phân bố xung quanh khuôn vòng và con lăn áp lực được lắp bên trong khuôn vòng. Con lăn áp lực được kết nối với trục chính truyền động và khuôn vòng được lắp trên giá đỡ cố định. Khi trục chính quay, nó sẽ truyền động cho con lăn áp lực quay. Nguyên lý hoạt động: Đầu tiên, cơ cấu vận chuyển vận chuyển vật liệu sinh khối đã nghiền thành kích thước hạt nhất định (3-5mm) vào buồng nén. Sau đó, động cơ truyền động trục chính để dẫn động con lăn ép quay, con lăn ép di chuyển với tốc độ không đổi để phân tán đều vật liệu giữa con lăn ép và khuôn vòng, khiến khuôn vòng nén và ma sát với vật liệu, con lăn ép với vật liệu, và vật liệu với vật liệu. Trong quá trình ép ma sát, xenlulo và hemicellulose trong vật liệu kết hợp với nhau. Đồng thời, nhiệt sinh ra do ma sát ép làm mềm lignin thành chất kết dính tự nhiên, giúp xenlulo, hemicellulose và các thành phần khác liên kết chặt chẽ hơn với nhau. Với việc liên tục nạp vật liệu sinh khối, lượng vật liệu chịu nén và ma sát trong các lỗ khuôn tạo hình tiếp tục tăng. Đồng thời, lực ép giữa sinh khối tiếp tục tăng và liên tục cô đặc và hình thành trong lỗ khuôn. Khi áp suất đùn lớn hơn lực ma sát, sinh khối được đùn liên tục từ các lỗ khuôn xung quanh khuôn vòng, tạo thành nhiên liệu đúc sinh khối với mật độ đúc khoảng 1g/Cm3.
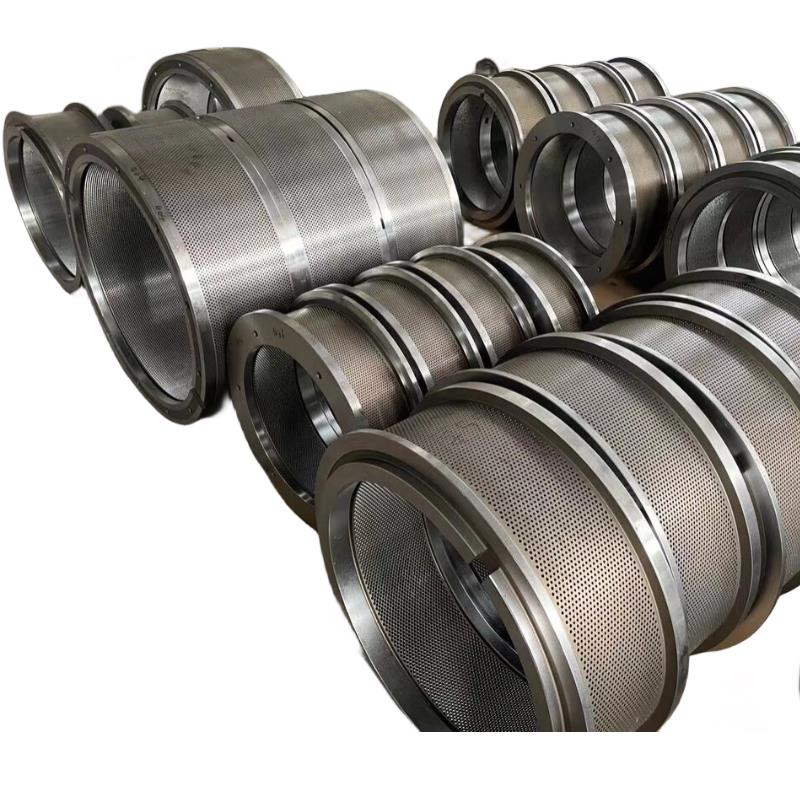
1.2 Sự mài mòn của khuôn đúc:Sản lượng máy đơn của máy ép viên lớn, có mức độ tự động hóa tương đối cao và khả năng thích ứng mạnh mẽ với nguyên liệu thô. Máy có thể được sử dụng rộng rãi để xử lý nhiều loại nguyên liệu sinh khối, phù hợp cho sản xuất nhiên liệu sinh khối đặc quy mô lớn và đáp ứng nhu cầu phát triển công nghiệp hóa nhiên liệu sinh khối đặc trong tương lai. Do đó, máy ép viên khuôn vòng được sử dụng rộng rãi. Do có thể có một lượng nhỏ cát và các tạp chất không phải sinh khối khác trong nguyên liệu sinh khối đã qua xử lý, nên rất có thể gây ra hiện tượng hao mòn đáng kể cho khuôn ép của máy ép viên. Tuổi thọ của khuôn ép được tính toán dựa trên năng lực sản xuất. Hiện tại, tuổi thọ của khuôn ép tại Trung Quốc chỉ từ 100-1000 tấn.
Sự hỏng hóc của khuôn vành khuyên chủ yếu xảy ra trong bốn hiện tượng sau: ① Sau khi khuôn vành khuyên hoạt động trong một thời gian, thành trong của lỗ khuôn tạo hình bị mòn và khẩu độ tăng lên, dẫn đến biến dạng đáng kể của nhiên liệu tạo hình được sản xuất; ② Độ dốc nạp liệu của lỗ khuôn tạo hình của khuôn vành khuyên bị mòn, dẫn đến lượng vật liệu sinh khối bị ép vào lỗ khuôn giảm, áp suất đùn giảm và lỗ khuôn tạo hình dễ bị tắc, dẫn đến hỏng khuôn vành khuyên (Hình 2); ③ Sau khi vật liệu thành trong giảm mạnh và lượng xả (Hình 3);
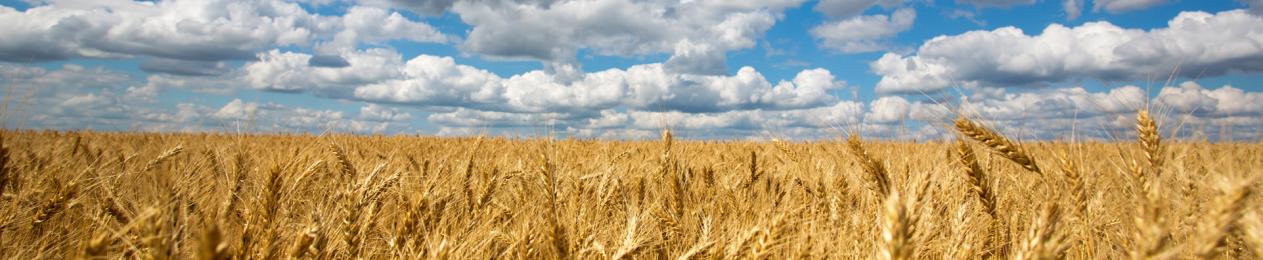
④ Sau khi lỗ bên trong của khuôn vành khuyên bị mòn, độ dày thành giữa các mảnh khuôn liền kề L trở nên mỏng hơn, dẫn đến độ bền kết cấu của khuôn vành khuyên giảm. Các vết nứt dễ xảy ra ở phần nguy hiểm nhất và khi các vết nứt tiếp tục mở rộng, hiện tượng gãy khuôn vành khuyên xảy ra. Nguyên nhân chính khiến khuôn vành khuyên dễ bị mòn và tuổi thọ sử dụng ngắn là do cấu trúc không hợp lý của khuôn vành khuyên (khuôn vành khuyên được tích hợp với các lỗ khuôn vành khuyên). Cấu trúc tích hợp của hai khuôn vành khuyên dễ dẫn đến hậu quả như sau: đôi khi chỉ một vài lỗ khuôn vành khuyên bị mòn và không thể hoạt động, toàn bộ khuôn vành khuyên cần được thay thế, điều này không chỉ gây bất tiện cho công việc thay thế mà còn gây lãng phí kinh tế lớn và tăng chi phí bảo trì.
1.3 Thiết kế cải tiến kết cấu khuôn định hìnhĐể kéo dài tuổi thọ khuôn vòng của máy ép viên, giảm hao mòn, dễ dàng thay thế và giảm chi phí bảo trì, cần phải thực hiện thiết kế cải tiến hoàn toàn mới cho cấu trúc khuôn vòng. Khuôn đúc nhúng đã được sử dụng trong thiết kế, và cấu trúc buồng nén cải tiến được thể hiện trong Hình 4. Hình 5 cho thấy mặt cắt ngang của khuôn đúc cải tiến.
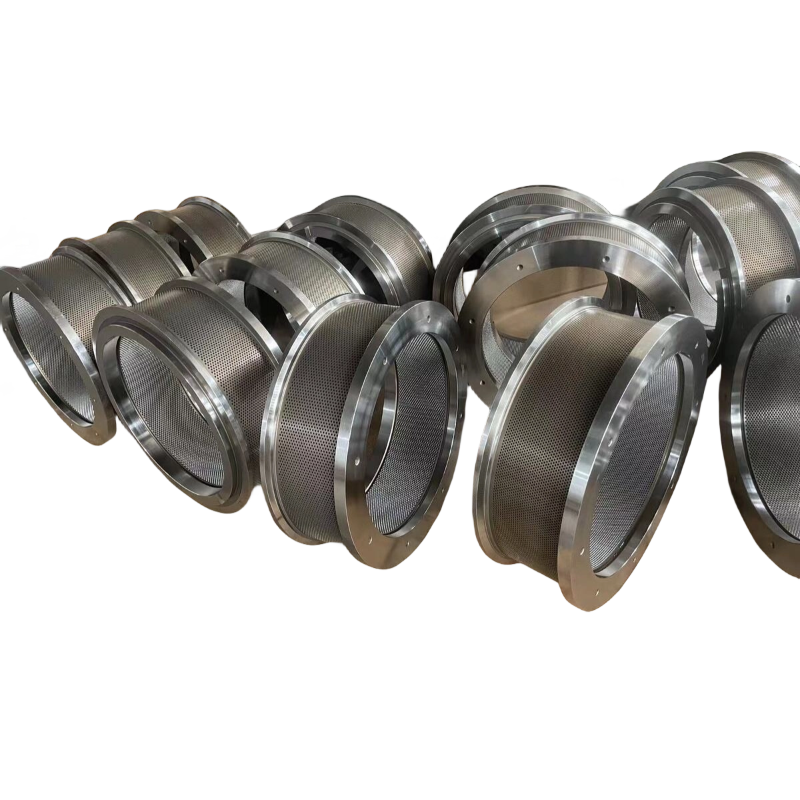
Thiết kế cải tiến này chủ yếu nhắm vào máy tạo hạt khuôn vòng với dạng chuyển động của con lăn áp lực chủ động và khuôn vòng cố định. Khuôn vòng dưới được cố định trên thân máy và hai con lăn áp lực được kết nối với trục chính thông qua một tấm kết nối. Khuôn tạo hình được nhúng vào khuôn vòng dưới (sử dụng khớp nối can thiệp) và khuôn vòng trên được cố định vào khuôn vòng dưới thông qua bu lông và kẹp chặt vào khuôn tạo hình. Đồng thời, để ngăn khuôn tạo hình bật lại do lực sau khi con lăn áp lực lăn qua và di chuyển theo hướng xuyên tâm dọc theo khuôn vòng, vít chìm được sử dụng để cố định khuôn tạo hình vào khuôn vòng trên và khuôn vòng dưới tương ứng. Để giảm lực cản của vật liệu đi vào lỗ và giúp vật liệu đi vào lỗ khuôn thuận tiện hơn. Góc côn của lỗ cấp liệu của khuôn tạo hình được thiết kế là từ 60 ° đến 120 °.
Thiết kế cấu trúc khuôn tạo hình cải tiến có đặc điểm là đa chu kỳ và tuổi thọ cao. Khi máy tạo hạt hoạt động trong một khoảng thời gian, tổn thất ma sát làm cho lỗ khuôn tạo hình lớn hơn và thụ động hóa. Khi khuôn tạo hình bị mòn được tháo ra và mở rộng, nó có thể được sử dụng để sản xuất các thông số kỹ thuật khác của hạt tạo hình. Điều này có thể đạt được mục tiêu tái sử dụng khuôn và tiết kiệm chi phí bảo trì và thay thế.
Để kéo dài tuổi thọ của máy nghiền và giảm chi phí sản xuất, con lăn áp lực sử dụng thép cacbon cao, mangan cao, có khả năng chống mài mòn tốt, chẳng hạn như thép 65Mn. Khuôn tạo hình nên được chế tạo bằng thép cacbon hợp kim hoặc hợp kim niken crom cacbon thấp, chẳng hạn như Cr, Mn, Ti, v.v. Nhờ cải tiến buồng nén, lực ma sát mà khuôn vành trên và vành dưới chịu trong quá trình vận hành tương đối nhỏ so với khuôn vành. Do đó, thép cacbon thông thường, chẳng hạn như thép 45, có thể được sử dụng làm vật liệu cho buồng nén. So với khuôn vành định hình tích hợp truyền thống, nó có thể giảm việc sử dụng thép hợp kim đắt tiền, từ đó giảm chi phí sản xuất.
2. Phân tích cơ học khuôn tạo hình của máy tạo viên khuôn vòng trong quá trình làm việc của khuôn tạo hình.
Trong quá trình đúc, lignin trong vật liệu được làm mềm hoàn toàn do môi trường áp suất và nhiệt độ cao tạo ra trong khuôn đúc. Khi áp suất đùn không tăng, vật liệu sẽ trải qua quá trình hóa dẻo. Vật liệu chảy tốt sau khi hóa dẻo, do đó chiều dài có thể được đặt thành d. Khuôn tạo hình được coi như một bình chịu áp lực, và ứng suất trên khuôn tạo hình được đơn giản hóa.
Qua phân tích tính toán cơ học ở trên, có thể kết luận rằng để xác định áp suất tại bất kỳ điểm nào bên trong khuôn tạo hình, cần phải xác định biến dạng chu vi tại điểm đó bên trong khuôn tạo hình. Sau đó, có thể tính toán lực ma sát và áp suất tại vị trí đó.
3. Kết luận
Bài báo này đề xuất một thiết kế cải tiến kết cấu mới cho khuôn định hình của máy tạo hạt dạng vòng. Việc sử dụng khuôn định hình nhúng có thể giảm thiểu hiệu quả sự mài mòn khuôn, kéo dài tuổi thọ khuôn, tạo điều kiện thuận lợi cho việc thay thế và bảo trì, đồng thời giảm chi phí sản xuất. Đồng thời, phân tích cơ học khuôn định hình trong quá trình hoạt động của nó cũng được thực hiện, cung cấp cơ sở lý thuyết cho các nghiên cứu tiếp theo trong tương lai.
Thời gian đăng: 22-02-2024